What is the principle of Electrical Discharge Machining (EDM)
We know that traditional machining methods like turning, milling, grinding, and drilling all involve tools that are harder than the workpiece. The essence of these processes is using a harder material to cut a softer one, somewhat like using a knife to cut vegetables or peel fruit.
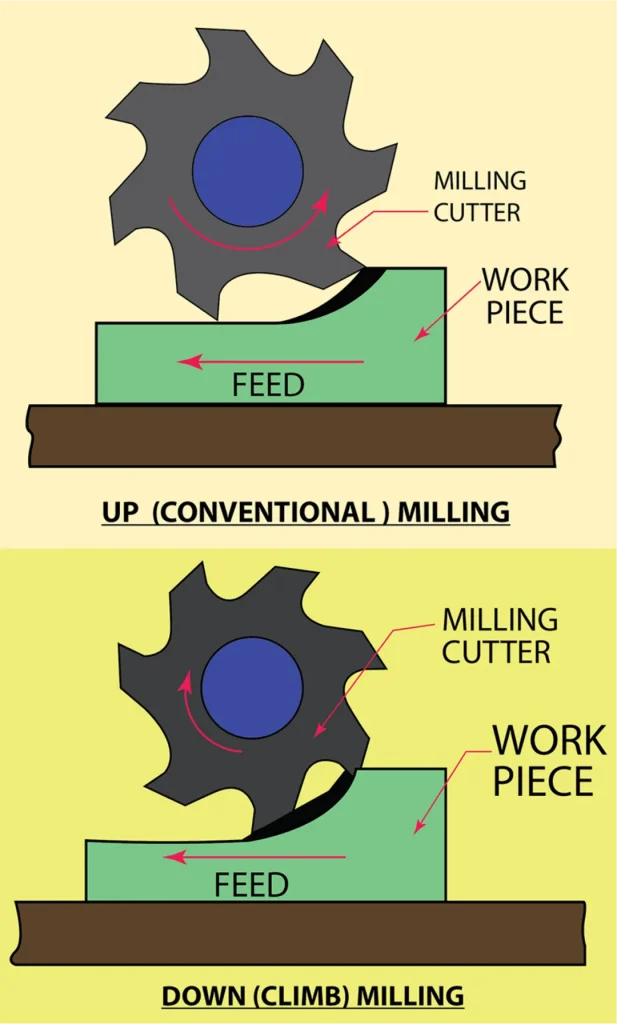
Milling Machining
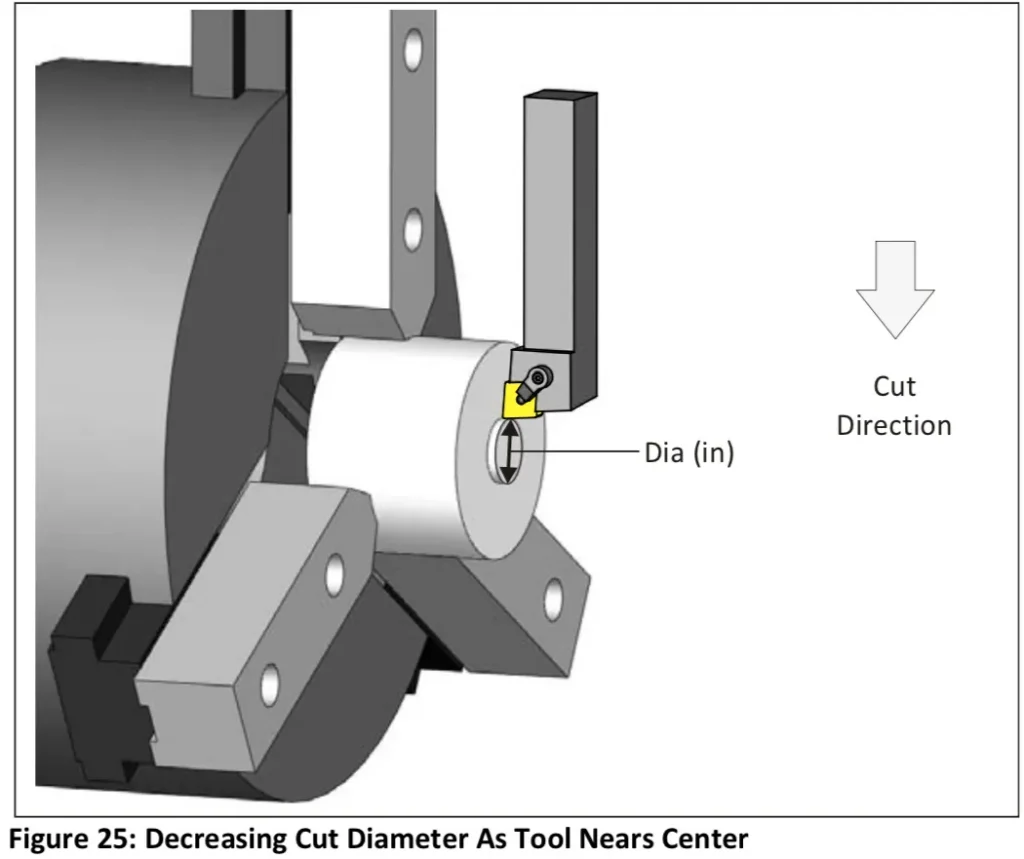
Turning Machining
However, Electrical Discharge Machining (EDM) is different. It can use softer tools, such as copper, to cut harder parts, like tool steel or carbide.
So, what is the principle of EDM, and why can soft tools machine hard materials? Let’s take a look at a diagram.
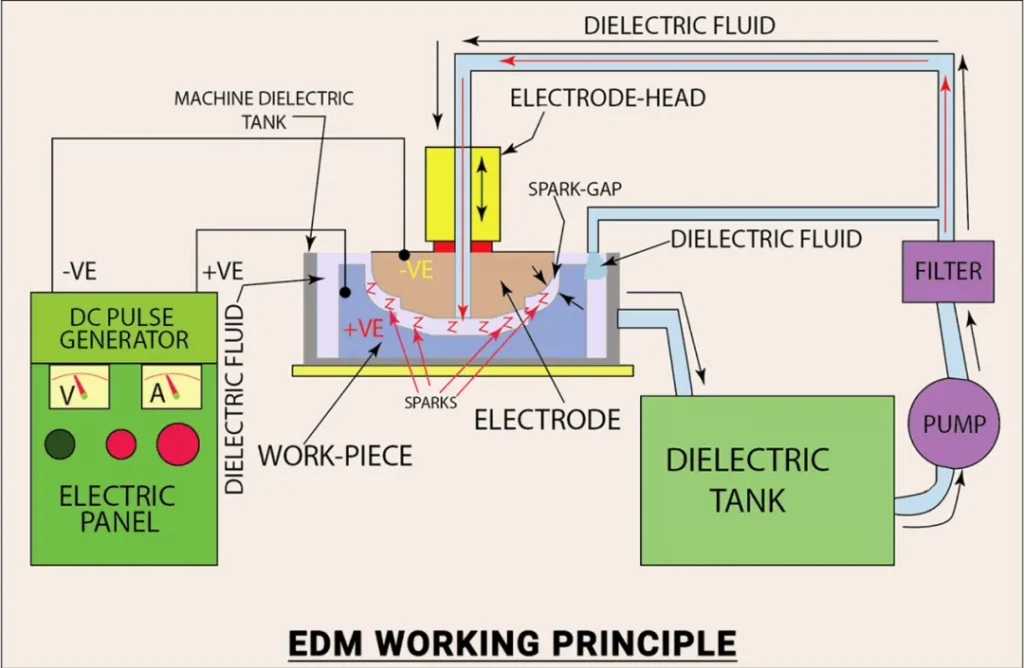
Diagram of the Principle of Electrical Discharge Machining (EDM)
In EDM, the tool does not physically contact the workpiece, meaning there is no interaction force as seen in traditional machining. As shown in the diagram, the tool serves as the electrode, and there is a gap between the tool and the workpiece, called the spark gap.
This gap is typically between 0.005 mm and 0.3 mm, and can sometimes reach up to 0.5 mm or even larger. Typically, the tool acts as the cathode, connected to the negative terminal of a DC pulse power supply, while the workpiece acts as the anode, connected to the positive terminal of the pulse power supply. The gap between the tool and the workpiece is filled with dielectric fluid.
When the tool approaches the workpiece, sparks are generated between the gap, producing extremely high electrical heat—up to 8,000–12,000°C—which melts and vaporizes part of the material on the workpiece surface. Thus, EDM is essentially a type of electrothermal erosion process.
On a microscopic level, the material that is melted is washed away by the dielectric fluid.

Principle of Electrical Discharge Machining (EDM)
Here, there are a few points that need clarification:
- How are sparks generated in EDM?
As the electrode approaches the workpiece, the electric field strength in the spark gap region exceeds the dielectric strength of the fluid at a certain point, causing the fluid to break down and become conductive. This allows the current to flow from the electrode (tool) to the workpiece in the form of sparks. - What is dielectric strength, and what is breakdown?
Materials can be classified as conductors, insulators, and semiconductors. Conductors allow electricity to pass through because they have many freely moving charged particles (carriers) that form a current when an external voltage (electric field) is applied. Insulators do not conduct electricity under normal conditions because their charge carriers cannot move freely. However, when the external electric field is strong enough, the insulator’s charge carriers become mobile, turning it into a conductor. Dielectric strength is the maximum voltage that an insulating material can withstand before it breaks down and becomes conductive.
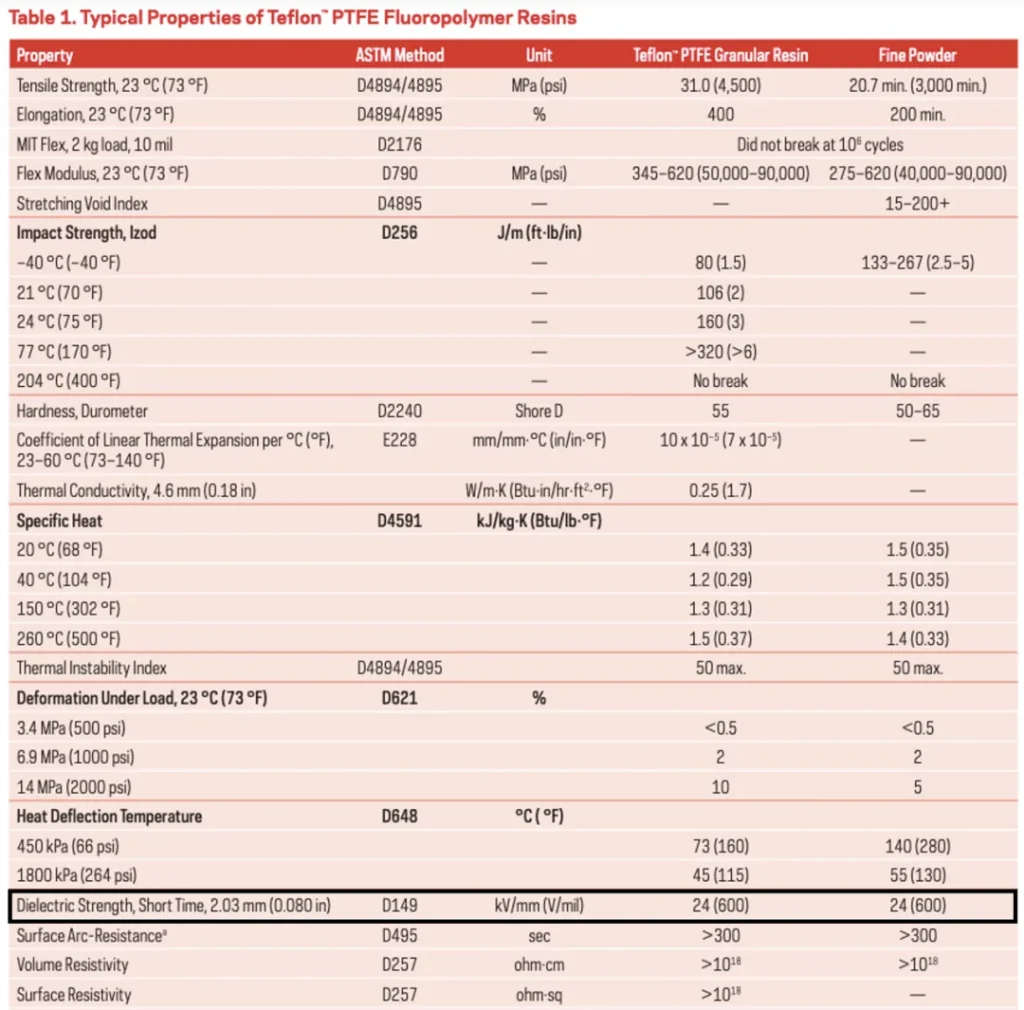
Teflon has a dielectric strength of 24 kV/mm, which means it can withstand up to 24 kV per millimeter before becoming conductive.
Once this threshold is exceeded, the insulator breaks down and conducts electricity. In EDM, when the pulse is applied, the dielectric fluid is broken down and becomes conductive, allowing the current to flow and be released as a spark. When the pulse stops, the dielectric fluid returns to its insulating state.
3. Why is high-frequency current needed?
High-frequency pulses are used because they provide brief on-times, which ensures the heat generated by the spark is insufficient to transfer deep into the tool or workpiece, thus protecting them. During the off-time, the dielectric fluid helps flush away the eroded material and replenishes the spark gap. This process happens very rapidly, with thousands or even tens of thousands of sparks occurring every second.
4. What are the common types of EDM?
The three main types are: Wire EDM, EDM drilling, and EDM sinking (molding).
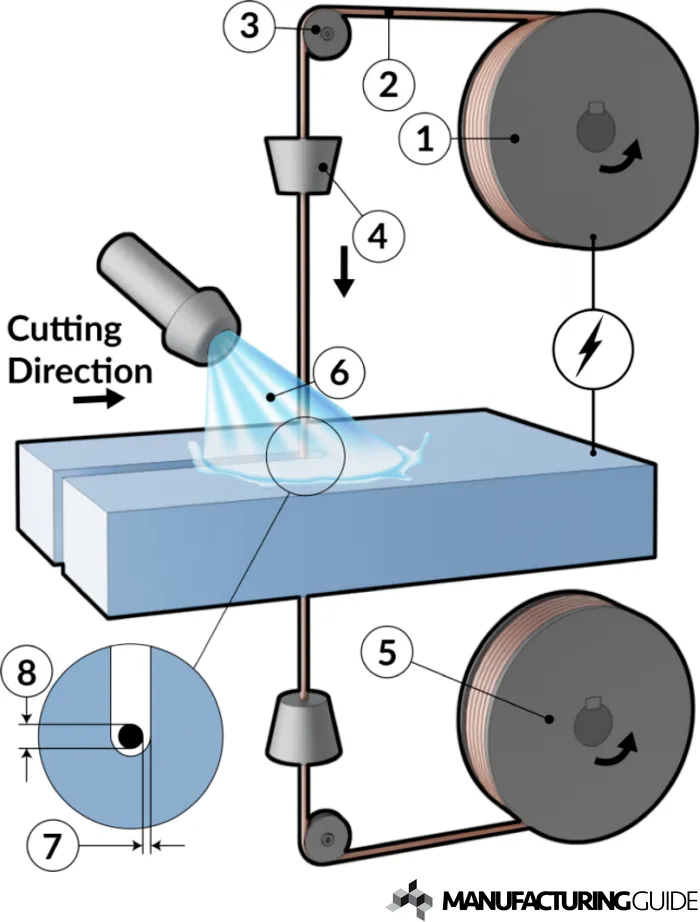
Wire EDM Principle: The fine wire in the wire EDM machine (made of brass, zinc-plated brass, or tungsten, with a diameter of 0.18 mm or 0.25 mm) acts as the electrode, while deionized water is used as the dielectric fluid (to make it insulating).
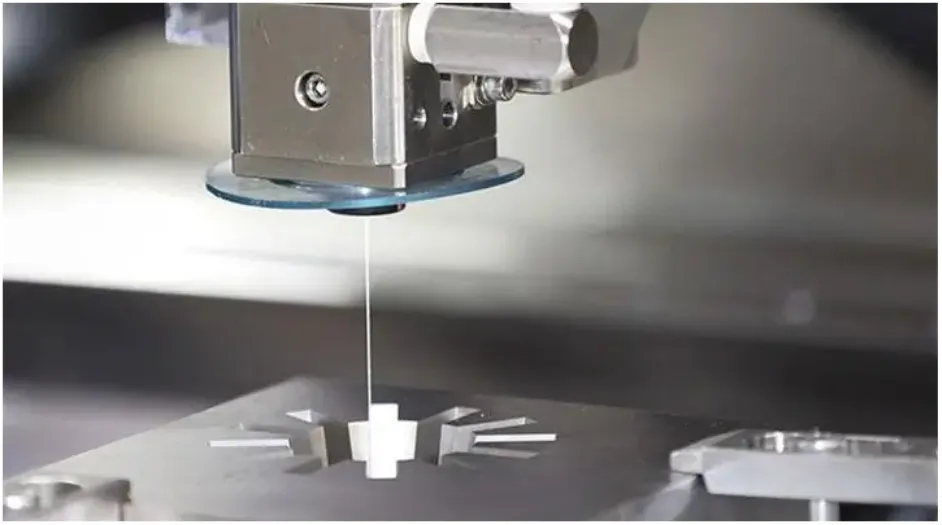
Diagram of Parts Processed by Wire EDM
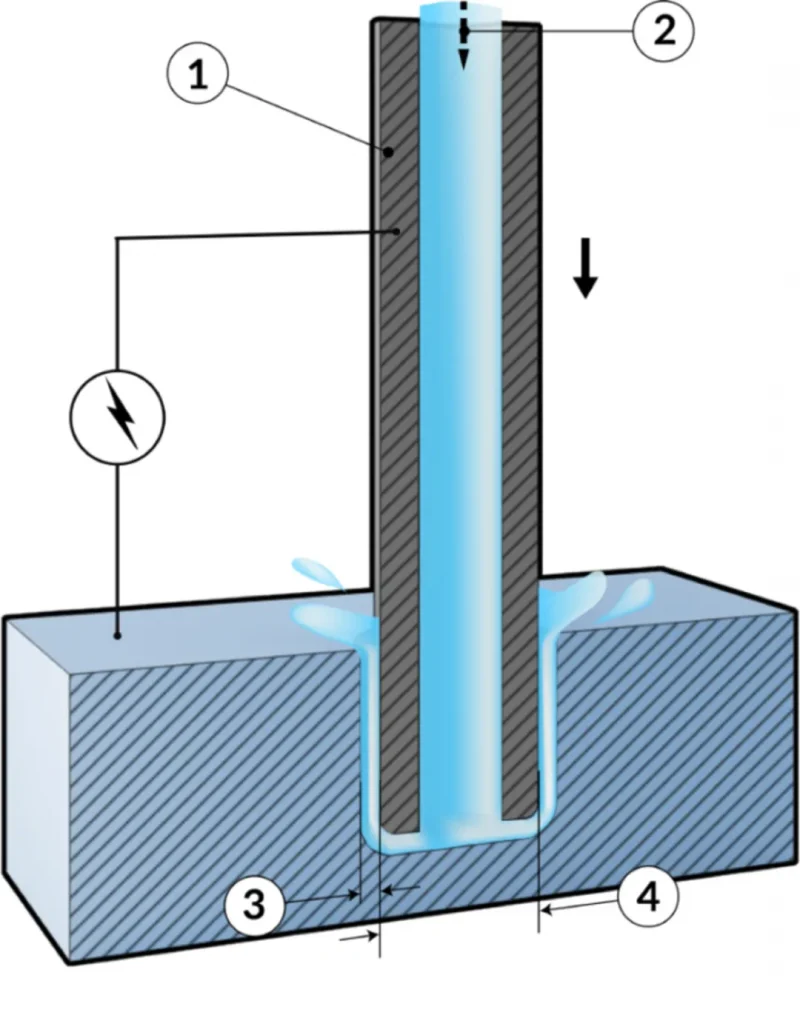
EDM Drilling Principle: A narrow nozzle near the workpiece creates intermittent sparks that melt and vaporize the material. The dielectric fluid, delivered through the nozzle, cools the process and helps flush away the material. The spark gap ensures that the hole’s diameter is slightly larger than the nozzle’s diameter.
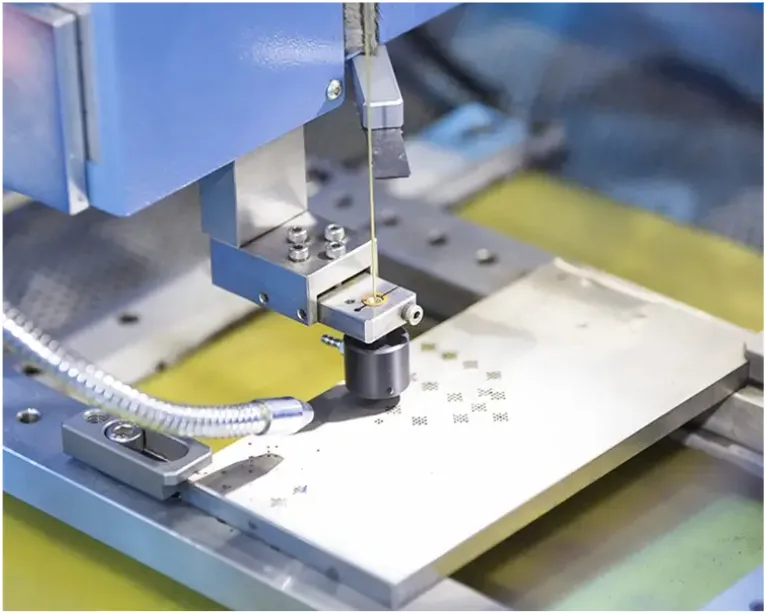
EDM Molding (Sinking): In EDM sinking, electrodes made from materials like copper, brass, graphite, tungsten, copper-tungsten, or carbide are used. This process is suitable for creating complex parts with high precision.
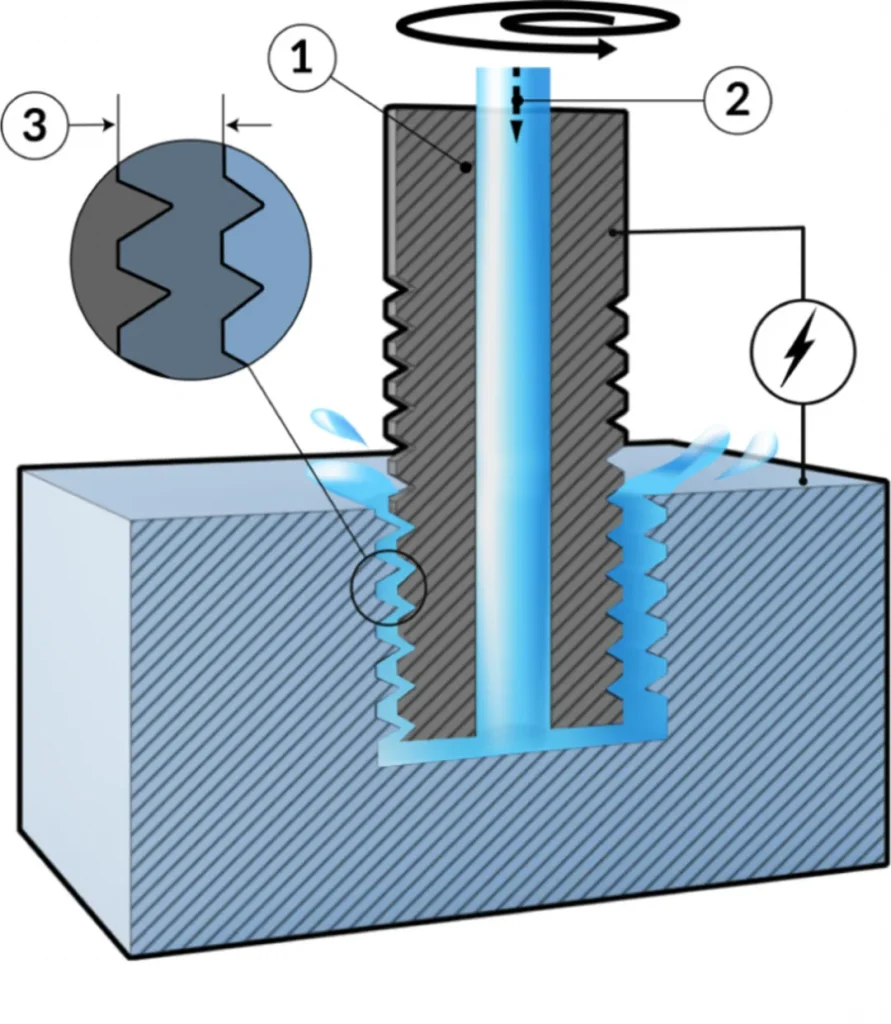
EDM Threaded Hole Machining
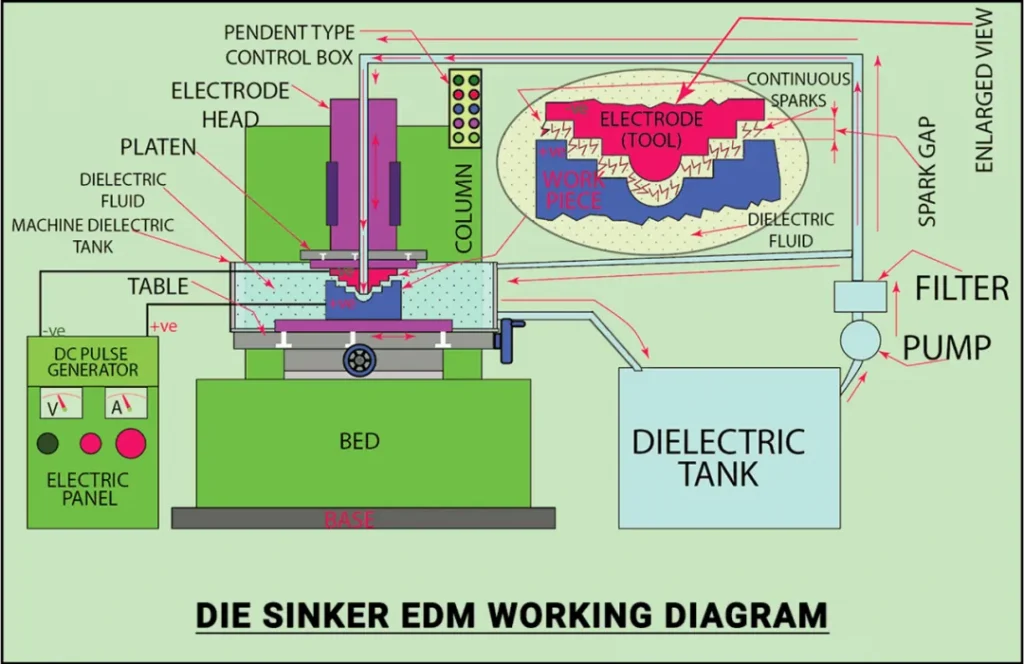
Diagram of the principle of EDM Molding (Sinking). To minimize electrode wear and maintain good surface finish quality, electrodes are typically made from materials such as copper, brass, graphite, tungsten, copper-tungsten, carbide, or copper-graphite.
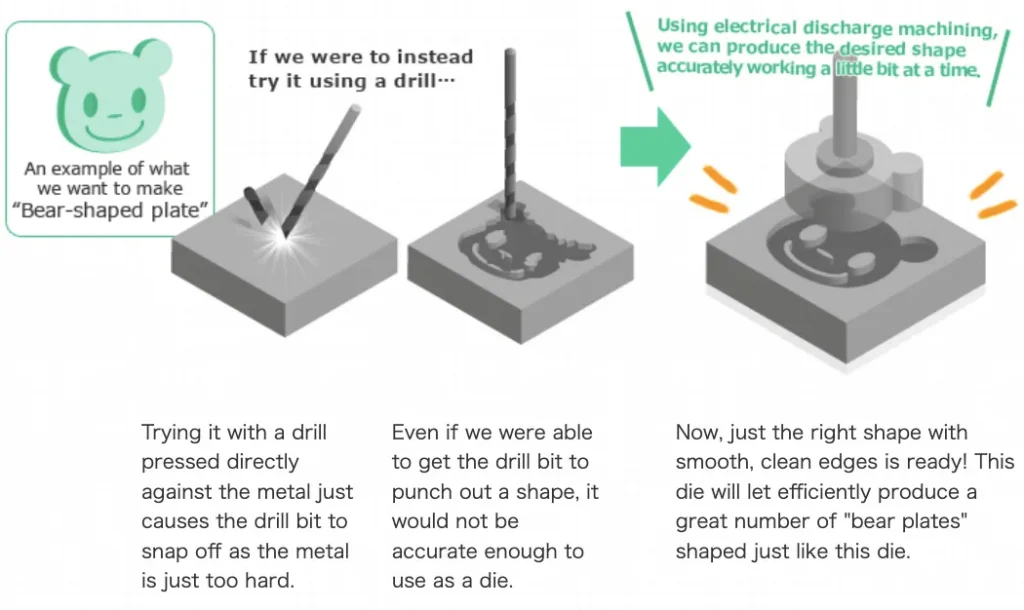
EDM Molding (Sinking): Copper or graphite can be used as electrodes, with specially designed tool shapes to machine complex parts. The left image shows a drill bit breaking due to the metal being too hard. The middle image shows insufficient precision, making the part unsuitable as a mold. The right image illustrates the use of EDM molding, where the desired high-precision mold is achieved in a single operation.
5. What materials can EDM machine?
EDM can theoretically be used on any conductive material. However, since the material removal rate is slower compared to traditional methods, EDM is best suited for machining hardened tool steels, titanium, carbide, tungsten carbide, chrome-nickel alloys, and other materials that are difficult to machine with conventional methods.
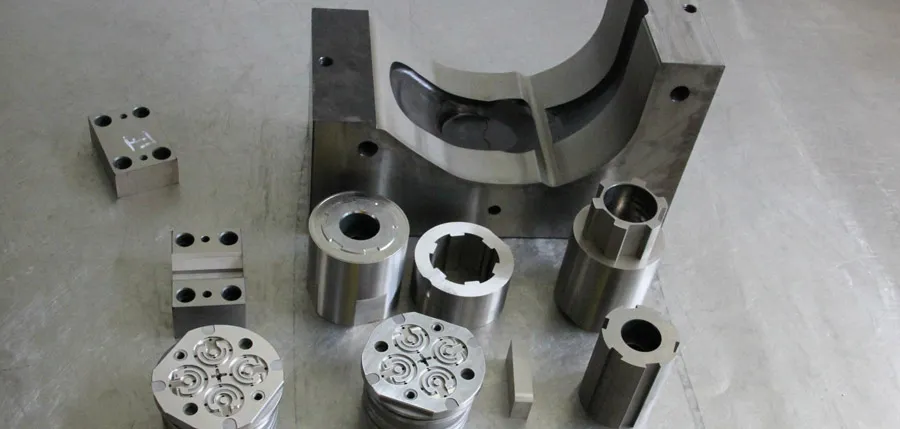
Electrical Discharge Machining (EDM) Parts
6. What is the accuracy of EDM?
EDM offers high precision. For example, wire EDM can achieve a precision of ±2.5 µm, with surface roughness as fine as 0.15–0.2 µRa. EDM sinking can achieve accuracy of ±0.05 mm to ±0.004 mm, and the surface finish on CNC machines can reach 0.29 µRa, with small machines achieving even finer finishes of 0.8 µRa.
7. What are the advantages and disadvantages of EDM?
Advantages:
- Wide material compatibility: It can machine any conductive material, regardless of its toughness, hardness, or microstructure.
- Suitable for hard materials: EDM can machine very hard conductive materials that are difficult to process using conventional methods.
- No deformation: There is no physical contact between the tool and the workpiece, so no cutting force is applied, avoiding material deformation.
- Capable of machining complex contours: Through molding EDM, precise contours can be replicated on the workpiece surface.
- High precision: EDM offers excellent surface finish and tolerance control.
- No burrs or tool marks: EDM does not leave burrs or tool marks on the workpiece surface.
Disadvantages:
- Not suitable for non-conductive materials.
- Slow material removal rate: The material removal rate is much slower compared to traditional machining processes, which can increase manufacturing time and overall costs.
- Higher cost: EDM machines require significant power consumption, making the process more expensive than conventional milling or turning.
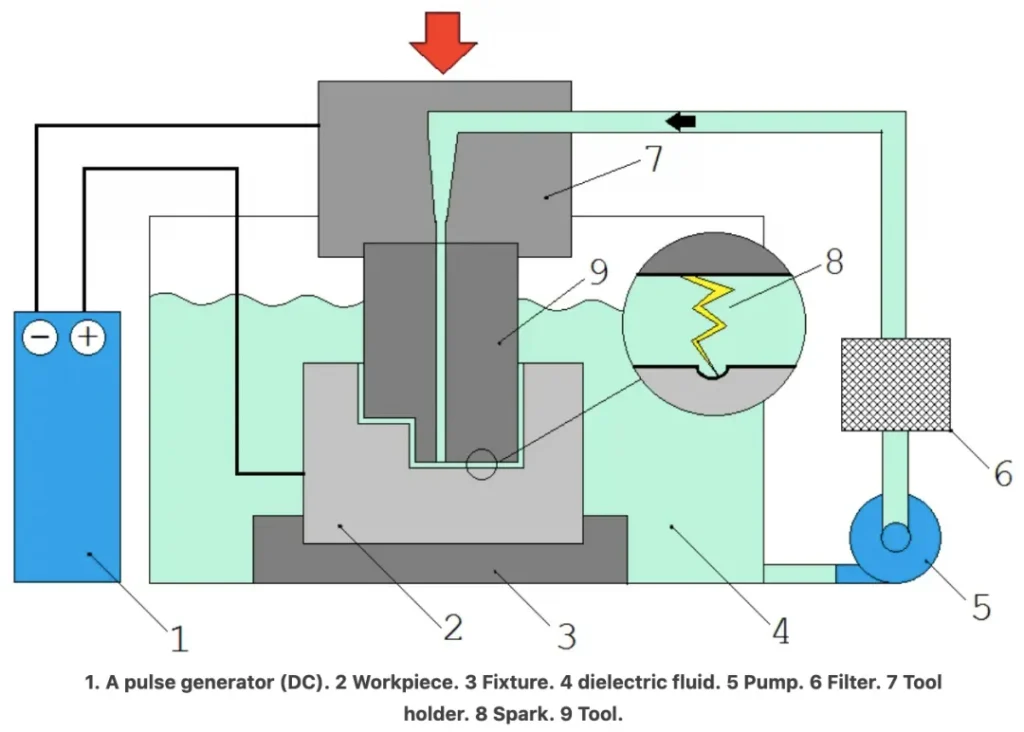
Diagram of the Electrical Discharge Machining (EDM) System
Since EDM directly uses electrical and thermal energy to remove metal, it is largely independent of the strength and hardness of the material being machined, allowing for soft tool electrodes to machine hard workpieces, effectively achieving “soft tools cutting hard materials.”
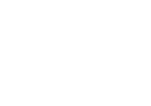