Common CNC Machining Issues: Do You Know How to Solve Them?
1. Overcutting of the Workpiece:
Causes:
- Tool deflection,The tool lacks sufficient strength or is too long or small, causing deflection.
- Operator error.
- Uneven cutting allowance (e.g., 0.5 mm left on the side of a curved surface, but only 0.15 mm left on the bottom).
- Improper cutting parameters (e.g., large tolerance, excessively fast SF setting).
Improvements:
- Tool selection principle: Use a larger, shorter tool when possible.
- Add a corner cleaning program and keep the allowance as even as possible (ensure the side and bottom allowances are the same).
- Adjust cutting parameters reasonably and round sharp corners in large allowance areas.
- Utilize the machine’s SF function and allow the operator to fine-tune the speed for optimal cutting performance.
2. Coordinate System Alignment Issues:
Causes:
- Inaccurate manual operation by the operator.
- Burrs around the mold.
- Magnetic centering rod.
- Mold sides are not perpendicular.
Improvements:
- Manual operation should be repeatedly checked, and centering should be done at the same point and height.
- Use a whetstone or file to remove burrs around the mold, wipe clean with cloth, and confirm by hand.
- Demagnetize the centering rod before use (ceramic centering rods or other alternatives can also be used).
- Check if the mold sides are perpendicular with a dial indicator (significant deviations should be discussed with the mold technician).
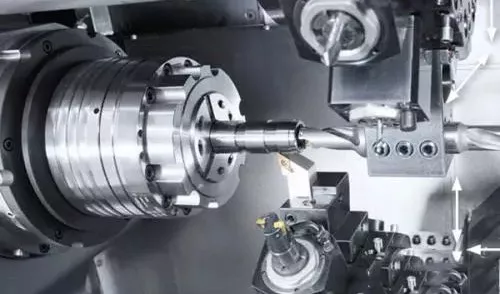
3. Tool Offset Issues:
Causes:
- Inaccurate manual operation by the operator.
- Incorrect tool clamping.
- Errors in the fly cutter blade (the fly cutter itself has some inherent errors).
- Discrepancies between R-tool, flat-end tool, and fly cutter.
Improvements:
- Manual operations should be thoroughly checked, and the same point should be used for tool setting.
- Clean the tool holder with an air gun or wipe with a cloth before clamping.
- Measure the tool holder when using a fly cutter; for flat surfaces, use only one blade.
- Create a separate tool-setting program to avoid discrepancies between R-tools, flat tools, and fly cutters.
4. CNC Crash – Programming
Causes:
- Insufficient or missing safe height (during rapid feed G00, the tool or chuck collides with the workpiece).
- Mismatch between the tool specified in the program sheet and the actual tool in the program.
- Incorrect tool length (cutting edge length) on the program sheet versus the actual machining depth.
- Discrepancy between the Z-axis values in the program sheet and the actual Z-axis readings.
- Incorrect coordinate settings during programming.
Improvements:
- Accurately measure the workpiece height and ensure the safe height is above the workpiece.
- Ensure the tool specified in the program sheet matches the actual tool (preferably use automated program sheets or include images).
- Measure the actual machining depth on the workpiece and clearly note the tool length and cutting edge length on the program sheet (typically, the tool holder should be 2-3 mm higher than the workpiece, with a clearance of 0.5-1.0 mm for the cutting edge).
- Use the actual Z-axis reading from the workpiece and note it clearly in the program sheet (this is usually done manually and should be checked repeatedly).
- Ensure the correct coordinate settings are used during programming.
5. CNC Crash – Operator:
Causes:
- Incorrect Z-axis tool setting depth.
- Incorrect centering or data entry (e.g., failure to account for tool radius when measuring from one side).
- Using the wrong tool (e.g., using a D10 tool instead of a D4 tool).
- Running the wrong program (e.g., running A7.NC instead of A9.NC).
- Incorrect manual control direction on the handwheel.
- Wrong direction during manual rapid feed (e.g., pressing +X instead of -X).
Improvements:
- Pay attention to the tool setting depth for different positions (bottom, top, analyzed surface, etc.).
- Repeatedly check centering and data entry after completing these steps.
- When clamping the tool, double-check it against the program sheet before installation.
- Run programs one at a time in sequence.
- Operators should improve their machine operation skills for manual control.
- Raise the Z-axis above the workpiece before moving during manual rapid feed.
6. Curved Surface Precision:
Causes:
- Inappropriate cutting parameters, resulting in rough surfaces.
- Dull tool edges.
- Tool clamping is too long, or the cutting edge is too far from the workpiece.
- Poor chip removal, air blow, or coolant flow.
- Programming feed path issues (try to use climb milling where possible).
- Burrs on the workpiece.
Improvements:
- Set reasonable cutting parameters, tolerances, allowances, and feed rates.
- Operators should periodically check and replace tools as needed.
- The tool’s extension length should be minimized as much as possible while meeting machining requirements, to avoid excessive tool overhang.
- For flat tools, R-tools, and round-nose tools, set appropriate speeds and feed rates.
- Burrs on the workpiece: This is directly related to the machine, tool, and feed path. Therefore, understanding the machine’s performance is crucial, and additional passes may be needed to remove burrs from the edges.